Product ID:571 60001-ACX
ABB model name :DSDP 140B
Directory Description :DSDP 140B counter board
DSDP140B communicates the starting signal of the scissors, the motion position of the cutting edge and other control parameters to the DCV700 system through the communication template DSDP140B to control the motor. There is an incremental encoder on the motor shaft for feedback of the cutting edge position.
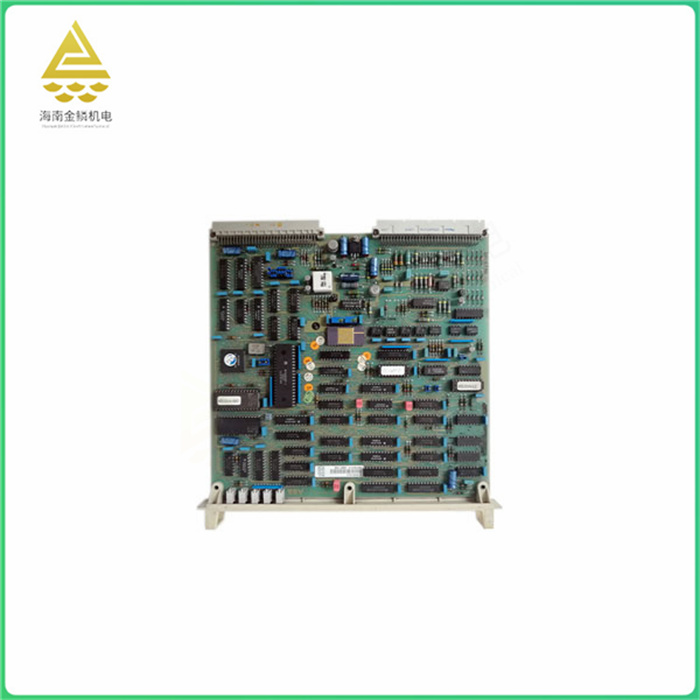
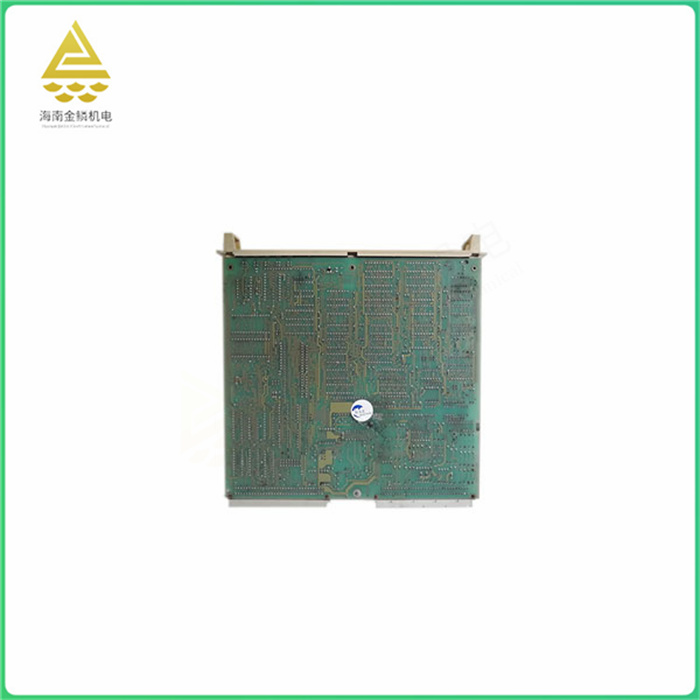
The control system detects the actual value of the motor position encoder through the positioning template DSDP140B. A counting template DSDP150 is connected to the DSDP140B board for starting the cutting edge. The positioning template DSDP140B sends the action time to the digital input template DSDI110 to participate in the control.
PLC reads the actual position of the scissors detected by the encoder through the element POSR_ H1 (read positioning template DSDP140B) and then forms the database and transmission communication through POSW_ H1 (write positioning template DSDP140B). If the steel is detected by the field inspection element, the length is integrated by the speed benchmark set by the operating station.
A Digital Servo Driver is a controller used to control a servo motor. It controls the speed, torque and position of the motor by receiving digital signals to achieve high-precision motion control. Digital servo driver usually adopts digital signal processor (DSP) or microcontroller (MCU) to realize the control algorithm, which has the advantages of high precision, high response speed and high stability.
Digital servo drives enable a variety of control methods, including position control, speed control and torque control. Among them, the position control usually adopts the pulse counting mode, and the rotation Angle of the motor is controlled by receiving the pulse signal. The speed control usually adopts the analog or digital input mode, by receiving the analog or digital signal to control the speed of the motor; Torque control usually adopts current control mode to control the output torque of the motor by controlling the current of the motor.
The digital servo drive also has overload protection, speed limit, position limit and other safety protection functions to ensure the safe operation of the motor. In addition, the digital servo drive can also realize the communication with the host computer, the motor running status, fault information and other data transmission to the host computer for monitoring and management.
In short, digital servo drive is one of the key components to achieve high-precision motion control, which is widely used in industrial automation, robotics, aerospace and other fields.
Digital servo drives have a variety of functions, including:
Control the rotation Angle or linear displacement of the motor to achieve the control of the motor position, so that the motor can move to the specified position according to the pre-set position parameters, so as to achieve the task of complex movement.
Control the speed of the motor to achieve the control of the motor speed, so that the moving object moves according to the predetermined speed, to achieve accurate speed control.
Control the torque or torque of the motor to achieve the control of the force applied to the moving object, so that the robot, the claw, etc., can move according to the predetermined force control parameters to complete the fine action.
It has the characteristics of high precision, high efficiency and good stability, which can ensure the stable movement of moving objects in complex environments, and improve the production efficiency and product quality of automated production lines.
It has overload protection, speed limit, position limit and other safety protection functions to ensure the safe operation of the motor.
To realize the communication with the host computer, the data such as the running state and fault information of the motor is transmitted to the host computer for monitoring and management.
In short, digital servo drive is one of the key components to achieve high-precision motion control, which is widely used in industrial automation, robotics, aerospace and other fields.
Digital servo drives have the following advantages:
High precision: digital servo system using digital signal control, with higher accuracy and stability, can meet the high-precision position, speed and torque control requirements.
Fast response speed: digital servo system uses digital signal transmission, has a faster response speed, can achieve fast control of the motor.
Programmable: Digital servo systems usually use microcontrollers or digital signal processors to achieve control algorithms, which can be programmed to achieve different control functions, with higher flexibility and scalability.
High reliability: The digital servo system uses digital signals for transmission and control, which is not susceptible to interference and damage, and has higher reliability and stability.
High safety: The digital servo system has overload protection, speed limit, position limit and other safety protection functions, which can ensure the safe operation of the motor.
Strong communication ability: the digital servo system can realize communication with the host computer, and transmit data such as the running state and fault information of the motor to the host computer for monitoring and management, and has stronger communication ability.
Good energy saving: the digital servo system can control the running state of the motor according to the need to achieve energy saving control, and has better energy saving performance.
In short, the digital servo drive has the advantages of high precision, fast response, programmability, high reliability, high safety, strong communication ability and good energy saving, and is widely used in industrial automation, robotics, aerospace and other fields.